Being a Professional Home Inspector can be a rewarding experience. As we’re not confined to an office, we get to experience a good bit of variety (sometimes too much…) in our job every day. We’re not locked into working with the same 17 people day after day and get to meet a wide range of individuals and deal with a diverse assortment of personalities. We get to earn a comfortable living (without having the debt that often comes along with earning an advanced college degree) and we get to help people for a living. We really can’t ask for more than that!
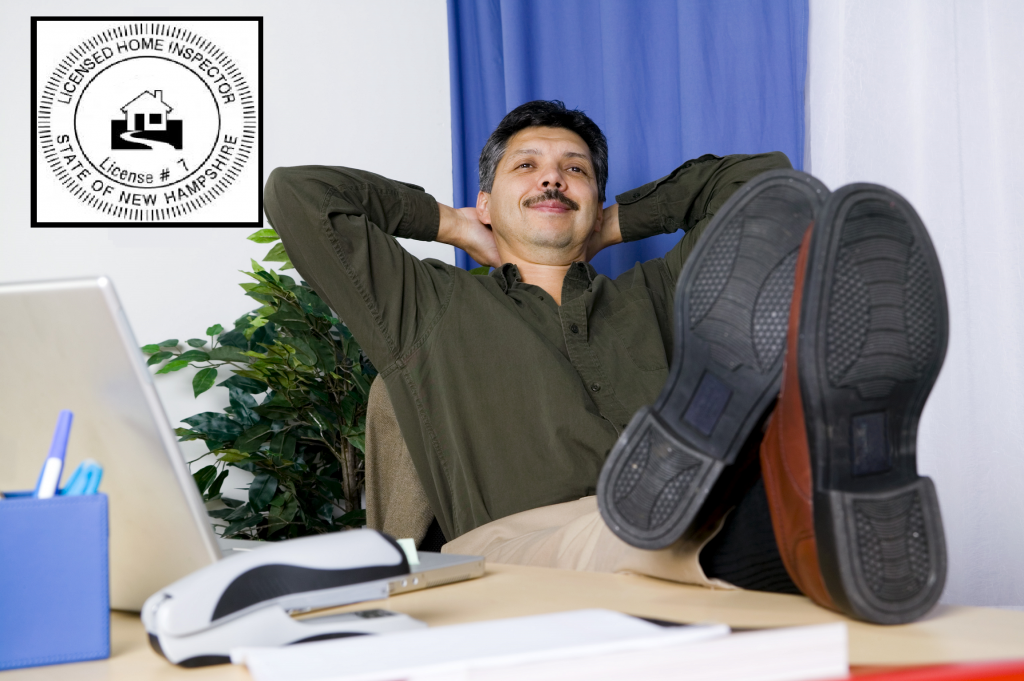
Well, if we really get down to it, we can ask for a little bit more than that. There are certain situations that we face as inspectors that could come with a bit more clarity. Often times, the rules that we follow can seem to be a bit at odds with common sense, and we’re left having to make a person decision as to which one of these “standards” we should follow.
Garage Door Safety Device Testing
Take, for example, testing garage doors. States that license home inspectors, as well as the two largest home inspection organizations, ASHI and InterNACHI, all require that inspectors test garage doors and their openers (allowing, of course, exceptions for doors and openers that are already damaged or unsafe). It’s pretty apparent that we’re responsible for testing these doors and their openers, if so equipped.
After checking to make sure that the door opens and closes properly, things get a little hazy. Some states and entities have Standards of Practice (SOP) language that specifically dictates how garage door safety device inspections are to be handled and some states and entities don’t get too specific about inspection of this type of equipment.
Since 1991, all garage door openers manufactured or imported for sale in the U.S. are required to have a pressure sensitive reversing system built into the device. Since 1993, a secondary entrapment protection system (like electric eye sensors) has also been required. (https://www.cpsc.gov/s3fs-public/garage.pdf)
SOP Examples
Some states have specific language in their SOP that specify how inspectors are supposed to handle testing of this safety equipment. Louisiana, for example requires that their inspectors test the electric eye sensor, but don’t require them to test the pressure reversing system.
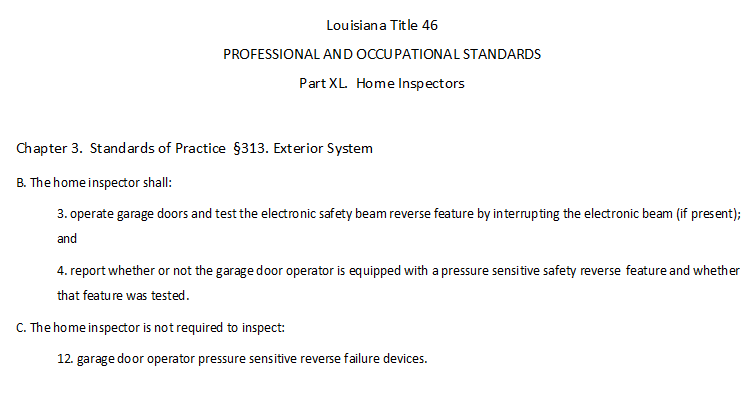
InterNACHI, currently the largest home inspector organization in the country, has requirements that match Louisiana, where testing of the electric eye is required but the pressure reversing system is excluded from an inspector’s duties.
Some states, like Texas and New Jersey, require that their inspectors test both the electric eye sensor and the pressure reversing system.
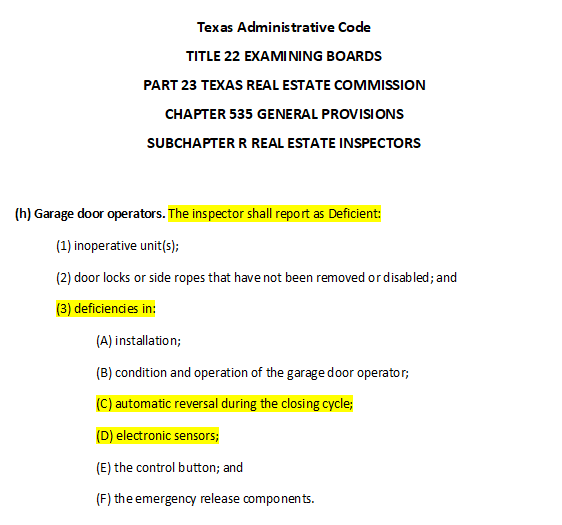
Some states, like Tennessee specify that an inspector must inspect the garage door operator and pressure reversing system, but don’t even mention the electric eye sensor.

And some states, like Alabama, and organizations, like ASHI, require inspectors to test garage door openers without even mentioning the pressure reversing system or the electric eye sensor directly. These entities either ignore them entirely (Alabama) or provide a general statement about inspectors not being required to operate “automatic safety controls” (ASHI).
In a Trick Bag
All these different standards indicate that, in more than a few situations, there really is no consensus across our industry about what it is that a Professional Home Inspector is required to do on their inspection. This lack of consensus can (at best) leave us wondering what’s the right thing to do to protect our clients and (at worst) provide ammunition for a resourceful plaintiff’s attorney to question our methods and standards in a court case.
So, what’s a professional to do?
It’s pretty apparent that there are a lot of divergent opinions out there when it comes to how thorough we should be when performing a home inspection. There will always be a faction of inspectors that truly believe that their clients don’t deserve anything more than the minimum effort required by the standards. And if that’s your gig, more power to you. I don’t harbor any ill will towards the minimalist inspectors. As long as you’re providing the minimum required services, dictated by your standards, and you’re following the laws of your state, you’re golden. If “do what I have to do and grab the check” is your business mantra, it’s your prerogative to conduct business that way and I won’t waste a minute of my time stressing over your business model.
No matter what industry we’re discussing, there will always be businesses that operate at either end of the spectrum. Some offer their clients the bare minimum, while others go way over the top to provide their customers with the best possible product and experience available. I prefer to work on the far end of the spectrum, wowing my clients with all the bells and whistles that I can work into my inspection product. But that’s just how I run my business, and there’s no requirement that anyone else do what I do.
As long as you’re obeying the laws of your state and/or the requirements of your inspection association, you’ve met the minimum requirements of your job.
But the odds are that if you fall into the “bare minimum” category, you’re probably not reading this article anyway. So, what I’m about to say really doesn’t concern you. My target audience is the inspector that’s looking out for the best interests of his/her client. A professional who’s striving to provide the highest quality product for their customers and hoping to use that extra perceived value to grow a successful inspection business. Someone who wants to be proud of their accomplishments and to be able to sleep at night with a clear conscience.
Do We Take the Risk?
What’s an inspector like that supposed to do in situations like these? Do we simply follow the guidelines and move on, or do we take a little risk, accept a bit more responsibility, and step out of our comfort zone to protect our clients?
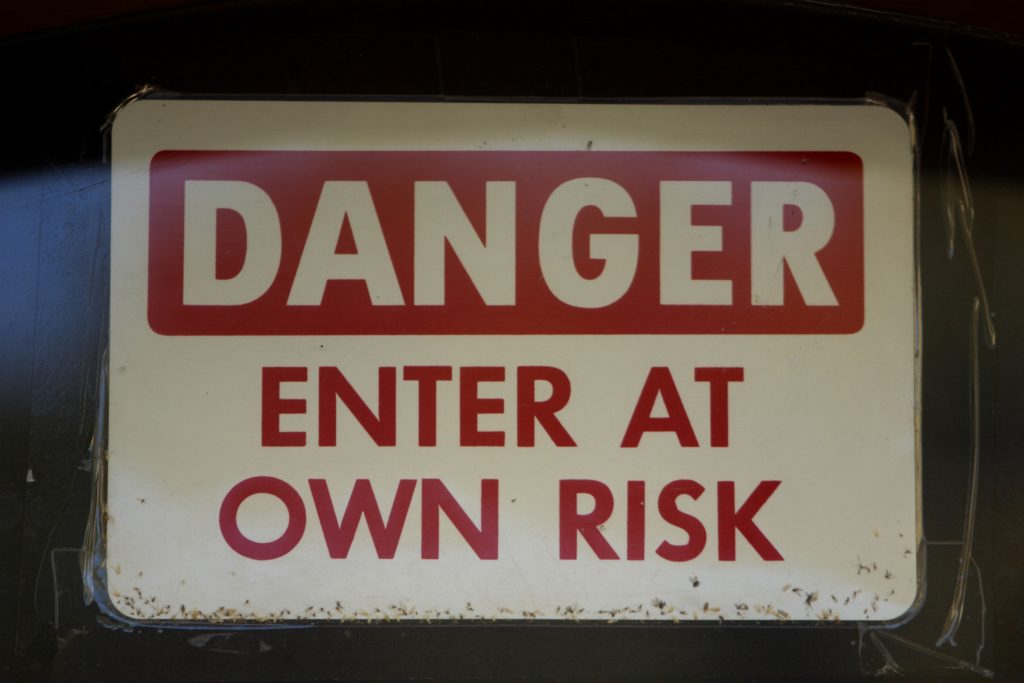
Risk is a tricky thing, especially in business. In order for us to accept some additional risk in our business, we’ve got to believe that there’s some tangible benefit to taking on that burden. Taking risk for risk’s sake may be fine when you’re on vacation, trying to decide if you want to bungee jump off a bridge, but taking a risk with no discernable benefit in your business is a dumb thing to do. (Some people may argue that bungee jumping off a bridge is a dumb thing to do too, but that’s a discussion for another day…)
I always try to follow my conscience when deciding how far to go in my inspection. In the case of inspecting garage door safety features, I ask myself how I would feel if one of my clients’ children were injured (or worse) because I didn’t want to take an extra two minutes (and accept a little bit of a risk) to check the safety features. Consumer Products Safety Commissions maintains a database (the National Electronic Injury Surveillance System) that monitors injuries from things like garage doors. It’s estimated that over 15,000 people a year are treated in emergency rooms from garage door injuries. Many of those treated are children, and it’s estimated that about three children die each year from garage door accidents.
I know that there’s a slight possibility that I may end up damaging a garage door by testing a pressure reverse feature isn’t functioning properly, but that’s a risk I’m willing to take in order to provide my clients with a quality inspection (and to help me sleep at night.)
Taking the Plunge (Prepared)
Now that’s not to say that I’m going to jump into a risky situation without arming myself with as much knowledge as I can. I’m going to make sure that I’ve educated myself on the situation, and I’m going to do everything possible to mitigate any possible risk from my job. As Benjamin Franklin said, “an ounce of prevention is worth a pound of cure.”
Arming ourselves with knowledge is one of the best things we can do. Knowing industry standards can provide us with an understanding of how to do things correctly as well as provide ample ammunition to defend ourselves if necessary. A quick internet search will often provide all the information needed to allow us to do our job properly, protecting our clients and our business at the same time.
Chamberlain, one of the largest manufacturers of garage door openers, provides clear guidance on testing the pressure reverse feature on their website’s support page.
Genie, another major player in the garage door industry, includes testing instructions in their operation manual, and even goes so far as to say that the pressure reverse mechanism must be tested each month.
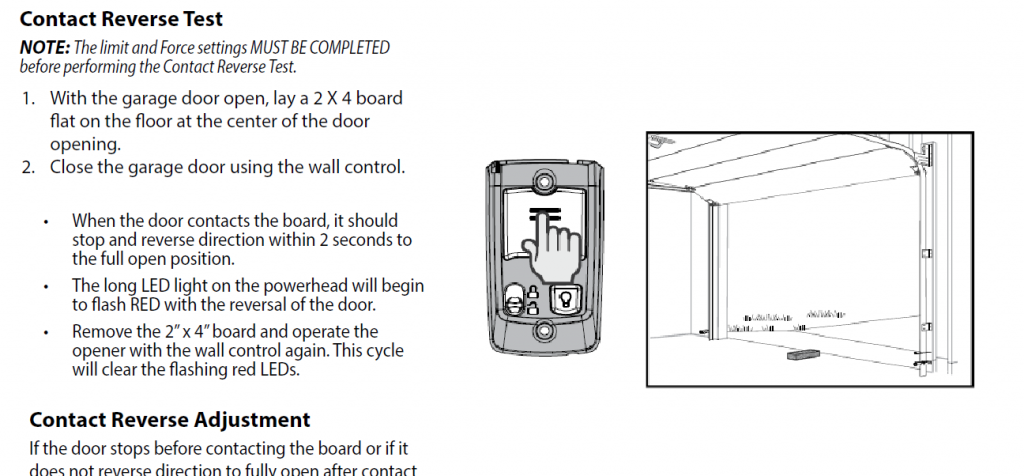
Craftsman also includes testing instructions and maintenance requirements in its garage door opener owner’s manual.
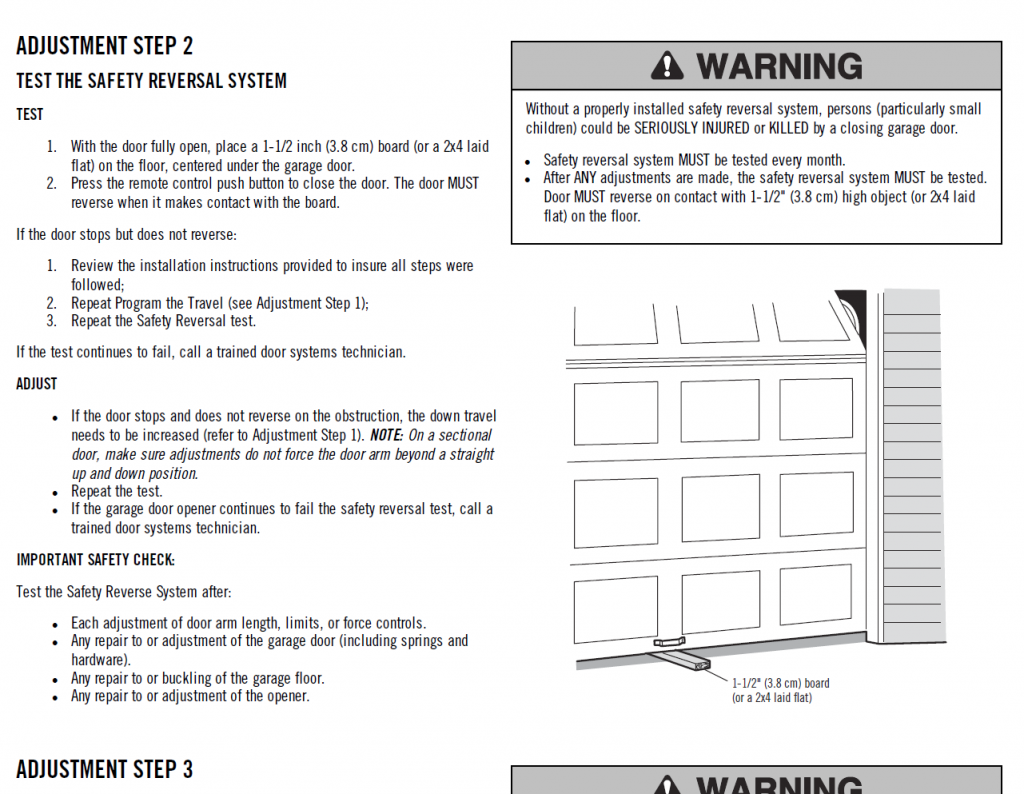
It’s Up to Us
Going above and beyond any of the Standards of Practice always entails some risk, and it’s up to us, as professionals and business owners, to decide what’s an acceptable level of risk when we’re performing an inspection.
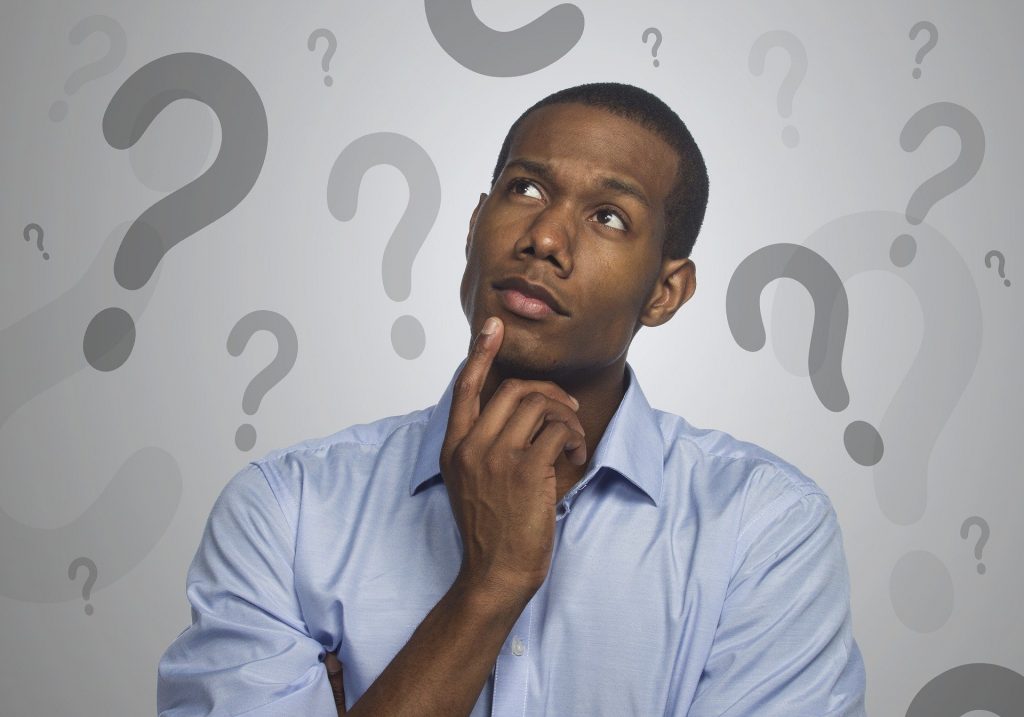
Each house is different, each client is different, and each situation is different, and each different situation calls for a different response. We bear the responsibility for make these decisions. And while there’s no right or wrong call, it’s up to us to gather as much information as we can in order for us to make the best decision possible to benefit our clients and our business, both now and in the future.
I welcome all feedback (both positive and negative) on this post.
Please take a moment to leave a comment below. Thank you!
Want to be an Influencer in Your Field? Share This Post!
Thanks, Joe
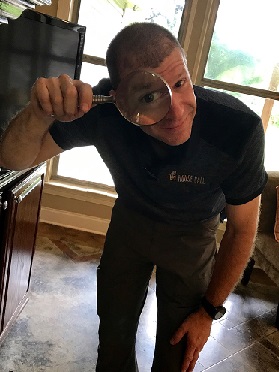